OTEC Drag Finishing Solutions and Advantages
2021-01-04 08:37:19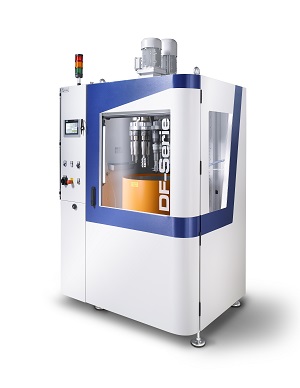
In the drag finishing process, the workpieces are clamped in specially designed holders. These holders are dragged in a circular motion through a process drum containing grinding or polishing granualate. This high-speed motion generates high contact pressure between the workpiece and the media, which in a very short time produces perfect results in the form of high-precision edge rounding, smoothing or a mirror finish in a quality equivalent to that obtained by manual polishing.
For Which Sectors Drag Finishing Can Be Preferred?
The OTEC drag finishing process is predestined for the finishing of large or heavy workpieces which cannot be finished in bulk. The workpieces are clamped in rotating holders and dragged through the process media at high speed. The high contact pressure and relative velocity between the workpiece and the process media gives perfect results in a very short time.
Drag Finishing can be preferred by every sector with its superior surface finishing quality. Some of these:
- Medical, dental industry,
- Pharmaceutical industry,
- Metal industry,
- Form and cutting tool manufacturers,
- Aviation, automotive industry,
- Optical and watch industry.
OTEC Drag Finishing Advantages
The advantages of OTEC Drag Finishing machines equipped with superior German technology:
- Stable workpiece surface quality.
- Removes processes such as robot polishing, CNC, EDM,hand polishing used in cast products. It reduces the workpiece to Ra: 0,01 µ surface roughness.
- It eliminates labor and human factors, thus obtaining uniform results, preventing possible errors, and reducing labor costs to zero.
- Different parts can be treated with similar processes and parameters.
- Eliminates high operating costs caused by solutions such as robot units and finishing bands.
OTEC conducts thousands of tests every year in its laboratories in Germany, and in cooperation with universities, attaches great importance to R&D studies. OTEC, the world leader in deburring and polishing, owes this to combining its years of know-how with science.